Terminology notwithstanding, my 1967 arched-back F-50R is a rosewood laminate, but the base wood (middle wood in the "sandwich") is definitely *not* rosewood, guys. You can see this in the picture of the endpin hole where the inner and outer layers are distinct from the lighter middle. While this this is evidence only about the sides of the guitar, I assume the back is laminated the same way. Hans has already shown through the magic of photography that one of the other '67 arched rosewood backs that he has in his archives in fact had to be thin veneers which were definitely sliced from the same log as mine.
Are you guys certain that your laminated arched mahogany backs are actually multi-ply mahogany? Does anyone have an endpin picture of a D-15M to look at, or are the sides actually solid? I'm just curious.
Hans, is my '67 Hoboken example of arched lamination just too unique to be compared with the rest of the product line? I kinda' thought from our earlier discussions that perhaps this was similar to the process that they were using on the arched-laminated maple F-50s of the time. Is that incorrect (I wouldn't be surprised)?
Are you guys certain that your laminated arched mahogany backs are actually multi-ply mahogany? Does anyone have an endpin picture of a D-15M to look at, or are the sides actually solid? I'm just curious.
Hans, is my '67 Hoboken example of arched lamination just too unique to be compared with the rest of the product line? I kinda' thought from our earlier discussions that perhaps this was similar to the process that they were using on the arched-laminated maple F-50s of the time. Is that incorrect (I wouldn't be surprised)?
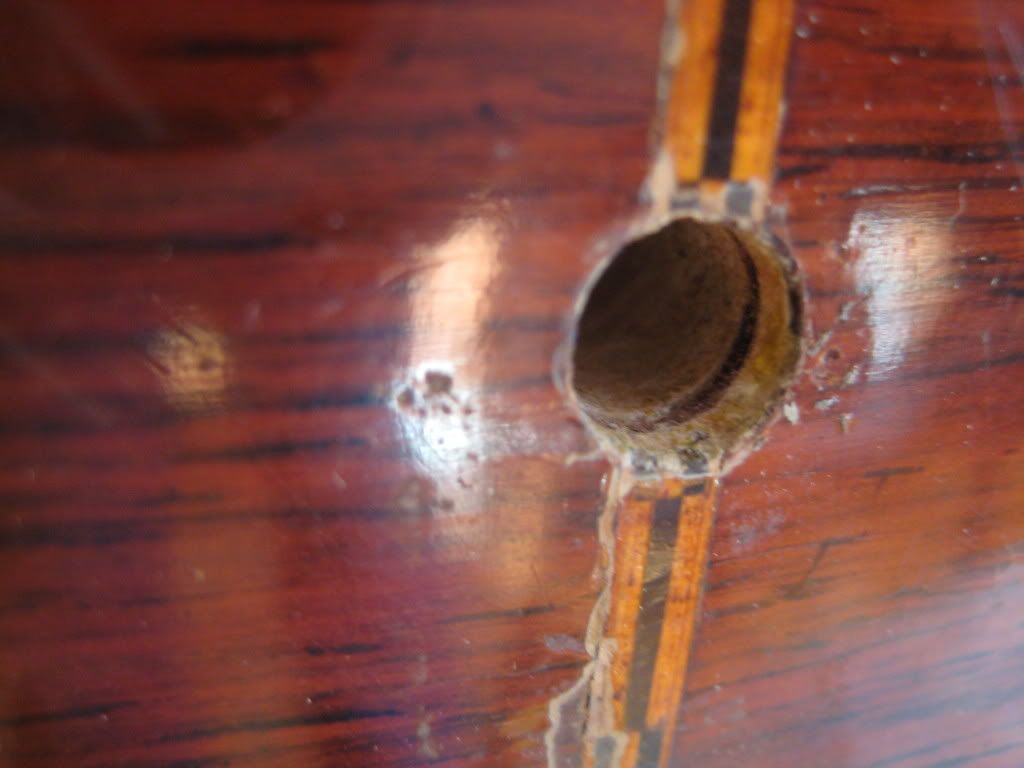