I have gained a perspective over time regarding the issue of neck resets on the acoustic guitar that I wanted to share. There is a commonly held belief that a neck reset is inevitable, at some point, as the forces working to implode the instrument will prove, eventually, to be greater than its overall structural integrity. For conventional construction, I believe this to be true and also hold that position. Mostly.
Under traditional (steel string) acoustic guitar design, a wooden block is glued to the intersection of the guitar back, sides and front/top/soundboard. The neck is then attached to this block. The strings, attached to and adjustable from the far end of the neck, are anchored to the soundboard via the bridge and, when tightened to 150+ lbs of tension, mostly provide audio bliss. Traditional design provides an effective compromise between rigidity and weight. Until it doesn't.
There is more than one factor at work that is contributing to my guitars need for a neck adjustment. Three factors are explored here:
Soundboard shear - Another culprit prompting a neck reset is soundboard shear, where the wood of the guitar top literally shears along the side(s) of the fingerboard extension (or neck block). This is evidenced by looking at the soundhole, where the section of the top that has shifted forward, toward the bridge, may be painfully visible. The neck block effectually rotates forward, also resulting in raised string ("action") height.
Potbelly bridge - The "belly" of the guitar is the prime real estate, that beachfront property (as luthier Kent Everett calls it) from the bridge to the tailblock. Our Guild "flattop" guitars are mostly flat across the soundboard. But not entirely. Luthier John Greven's adage, "No belly, no tone", is a true saying and indicates the need for a slight rise (or pull) of this lower bout area of the soundboard. This tension is audible: light tap your fingers across the soundboard, contrasting the area in front of the bridge to the area behind the bridge, to hear it. Too much belly probably means either bridge glue failure, bracing glue failure or, horror of horrors: insufficient construction (typically, vintage Guilds are rarely guilty of the latter).
For all three conditions, the saddle may be lowered to attempt to compensate for the increased string height. If the adjustments are minimal, all may be well. But, more often than not, the adjustments have a deleterious effect on the overall sound, as the "break" angle (measured from the saddle to the point of contact with the bridge) is reduced, the torque applied to the bridge/bridgeplate combination brace is reduced, and the output volume of the guitar is reduced. Asaddle bridge may be shaved (reduced in height), which may restore the break angle. But it will also reduce the mass of the bridge, which will alter the ability to "drive the top" (deliver the kinetic energy from the strings, via the bridge, across the soundboard). The guitar will sound different, usually NOT for the better.
Remediation - If the bridge or bracing has come unglued, apply glue and re-address the string height. At some point one may be left with no option but to reset the neck. If the bridge was shaved, replace it. If the soundboard has sheared, it must be cleated. Finally, the neck angle is addressed. The neck must be (carefully) removed, the angle of the heel adjusted, the joint shimmed or re-cut, the neck re-applied and any finish issues corrected.
For the lone guitar owner this may be a once-in-a-lifetime event. As challenging and upsetting as it may appear to be at the onset, I can assure you, "You and your guitar will be okay."
But imagine a world where neck resets have become a thing of the past, a non-issue... I believe proper adhesive selection to be an alternative to having to baby an instrument, temperature-wise. I believe soundboard shear to largely be a failure due to the flex potential in the soundbox design. By altering the design, the weakness can be eliminated. I believe potbelly bridges to be entirely avoidable. It is entirely feasible to be building instruments that do not require neck resets.
Here is an image showing the amount of flex in one of my Guilds that I took apart:
Under traditional (steel string) acoustic guitar design, a wooden block is glued to the intersection of the guitar back, sides and front/top/soundboard. The neck is then attached to this block. The strings, attached to and adjustable from the far end of the neck, are anchored to the soundboard via the bridge and, when tightened to 150+ lbs of tension, mostly provide audio bliss. Traditional design provides an effective compromise between rigidity and weight. Until it doesn't.
There is more than one factor at work that is contributing to my guitars need for a neck adjustment. Three factors are explored here:
- Neck block shift
- Soundboard shear
- Potbelly bridge
Soundboard shear - Another culprit prompting a neck reset is soundboard shear, where the wood of the guitar top literally shears along the side(s) of the fingerboard extension (or neck block). This is evidenced by looking at the soundhole, where the section of the top that has shifted forward, toward the bridge, may be painfully visible. The neck block effectually rotates forward, also resulting in raised string ("action") height.
Potbelly bridge - The "belly" of the guitar is the prime real estate, that beachfront property (as luthier Kent Everett calls it) from the bridge to the tailblock. Our Guild "flattop" guitars are mostly flat across the soundboard. But not entirely. Luthier John Greven's adage, "No belly, no tone", is a true saying and indicates the need for a slight rise (or pull) of this lower bout area of the soundboard. This tension is audible: light tap your fingers across the soundboard, contrasting the area in front of the bridge to the area behind the bridge, to hear it. Too much belly probably means either bridge glue failure, bracing glue failure or, horror of horrors: insufficient construction (typically, vintage Guilds are rarely guilty of the latter).
For all three conditions, the saddle may be lowered to attempt to compensate for the increased string height. If the adjustments are minimal, all may be well. But, more often than not, the adjustments have a deleterious effect on the overall sound, as the "break" angle (measured from the saddle to the point of contact with the bridge) is reduced, the torque applied to the bridge/bridgeplate combination brace is reduced, and the output volume of the guitar is reduced. A
Remediation - If the bridge or bracing has come unglued, apply glue and re-address the string height. At some point one may be left with no option but to reset the neck. If the bridge was shaved, replace it. If the soundboard has sheared, it must be cleated. Finally, the neck angle is addressed. The neck must be (carefully) removed, the angle of the heel adjusted, the joint shimmed or re-cut, the neck re-applied and any finish issues corrected.
For the lone guitar owner this may be a once-in-a-lifetime event. As challenging and upsetting as it may appear to be at the onset, I can assure you, "You and your guitar will be okay."
But imagine a world where neck resets have become a thing of the past, a non-issue... I believe proper adhesive selection to be an alternative to having to baby an instrument, temperature-wise. I believe soundboard shear to largely be a failure due to the flex potential in the soundbox design. By altering the design, the weakness can be eliminated. I believe potbelly bridges to be entirely avoidable. It is entirely feasible to be building instruments that do not require neck resets.
Here is an image showing the amount of flex in one of my Guilds that I took apart:
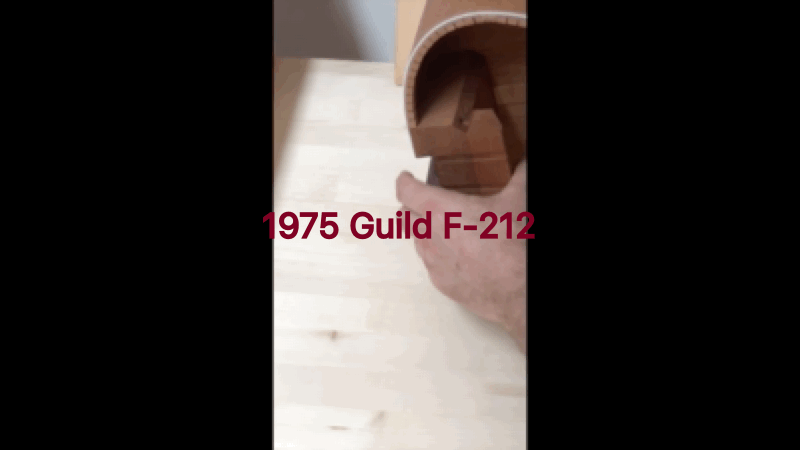
Last edited: