This 12 string had suffered the neck block shift and soundboard shear. The action was high and the sound output was… meh!
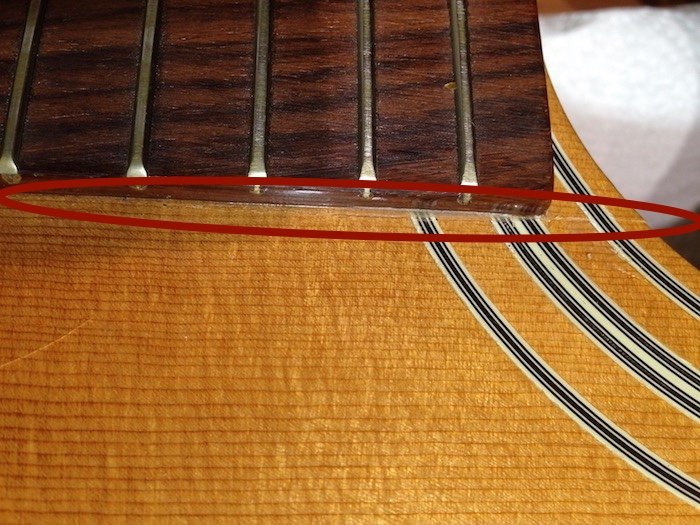
Staying true to my motto, “Why try to fix something when you can completely remake it,” I started taking this guitar apart. Being serious (for a few moments, anyway), I have no interest in living with the structural damage and loss of integrity of a soundboard shear. I equate it to a stress fracture in a jet engine mount. You don’t *have* to do anything about it, if you can successfully ignore it. I can’t successfully ignore it.
So I embarked on a journey to give this 12 string a makeover (which is, as of this writing, currently underway). I’ll post the highlights here. At the very least, I will be replacing the soundboard, bridge and fingerboard, so hang on...
I stared with the removal of the neck. Yes, you heard it right here: I took off a Guild neck. {gasp} It can be done! When I use steam (instead of a hot rod), I like to drill two holes, one on each side of the dovetail. This way I can rapidly alternate the application of the hot steam between either side of the neck joint, lessening the amount of water that will be introduced to the wood. Hot steam cools quickly and turns back to water. Water that has been infused with tiny particles of animal protein glue has a white-ish appearance. Ever seen those chalky looking rivulets inside your guitar? Guess what that tells you?
Actually, I missed my target on the first attempt, and had to re-drill. This why it is not a good idea to first determine that you are not going to be re-using certain components… it sets you up to be less careful.
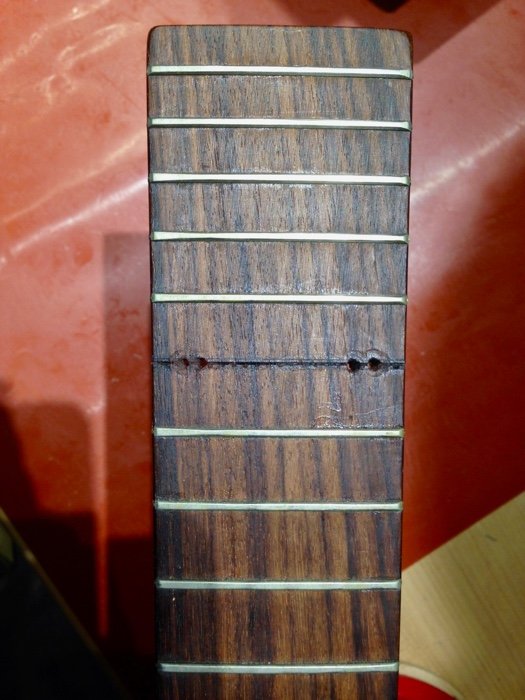
My first set of holes “Missed it by *that* much!"
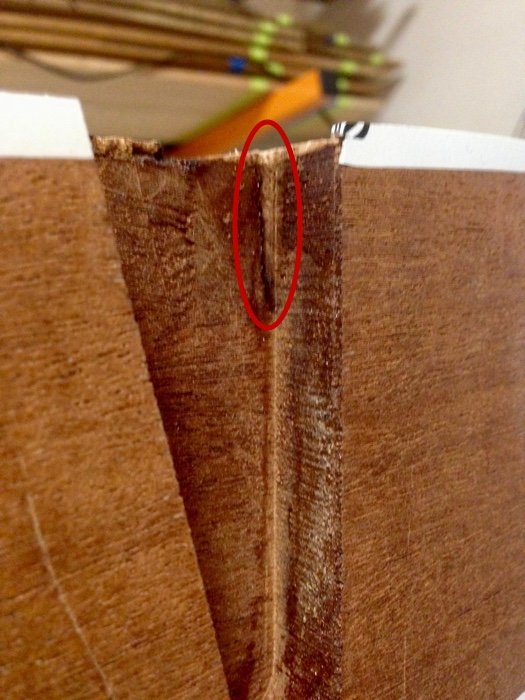
I removed the neck, curling the neck heel in the process. I had toyed with the idea of making a new neck for this guitar for a long time. I wanted to replace the twin compression rods with carbon fiber, and thin the grip substantially. This little mishap helped me make my decision… but I am getting ahead of my own story.
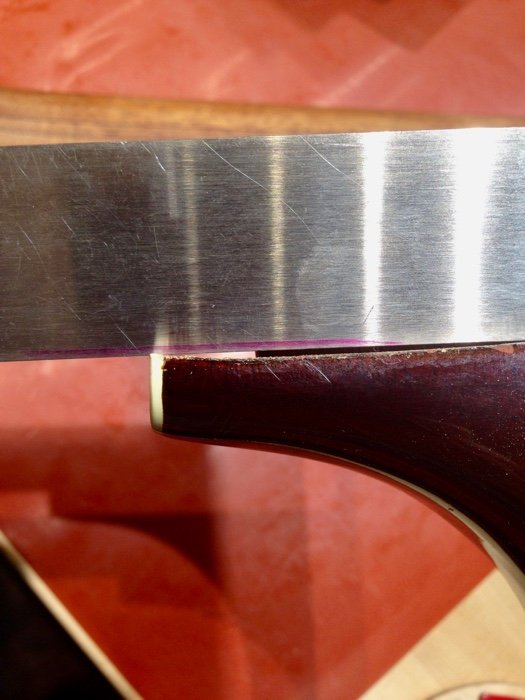
The fretboard extension is glued to the soundboard. When I remove a neck (such as for a neck reset), I apply heat to the area to soften the glue. Working slowly and carefully, using a spatula or two, I can work the bond loose between the (in this case) Spruce and the (in this case) Rosewood.
And sometimes you get a suprise under the lid:
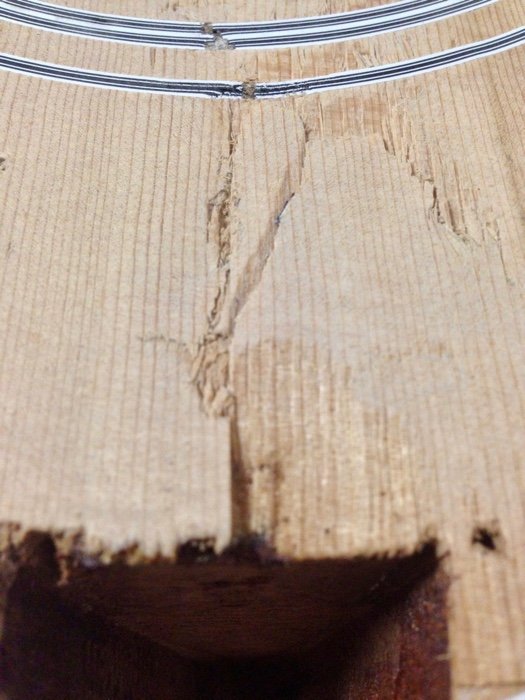
I am sure you are all familiar with the appearance of what we all lovingly refer to as “grain runout,” where one half of a soundboard looks darker that the other half (until you turn it upside down, and you see the reversal of the light/dark effect). Most of us can live with the aesthetic (or un-aesthetic) issue, but the greater concern of runout is structural integrity. The photo, above, shows how readily wood will release from itself when runout is severe, as I was so happy to discover was the case beneath the fingerboard extension. I knew there was something about this soundboard I didn’t like, something to account for its lackluster response. And that was before the shearing event occurred.
The guitar is now in two pieces: Neck and Body.
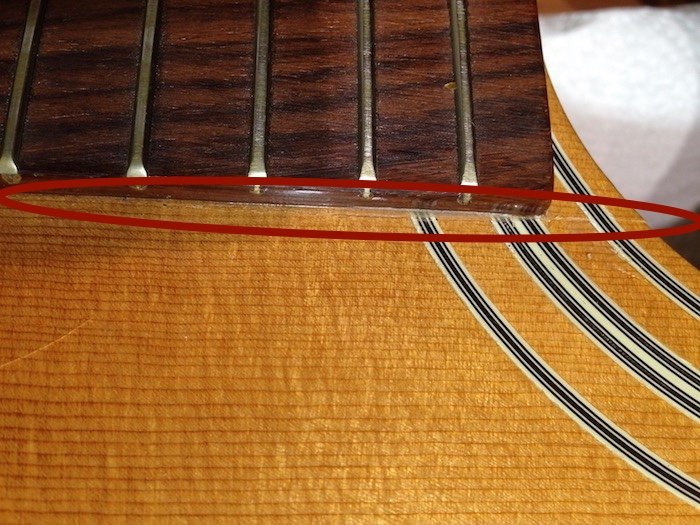
Staying true to my motto, “Why try to fix something when you can completely remake it,” I started taking this guitar apart. Being serious (for a few moments, anyway), I have no interest in living with the structural damage and loss of integrity of a soundboard shear. I equate it to a stress fracture in a jet engine mount. You don’t *have* to do anything about it, if you can successfully ignore it. I can’t successfully ignore it.
So I embarked on a journey to give this 12 string a makeover (which is, as of this writing, currently underway). I’ll post the highlights here. At the very least, I will be replacing the soundboard, bridge and fingerboard, so hang on...
I stared with the removal of the neck. Yes, you heard it right here: I took off a Guild neck. {gasp} It can be done! When I use steam (instead of a hot rod), I like to drill two holes, one on each side of the dovetail. This way I can rapidly alternate the application of the hot steam between either side of the neck joint, lessening the amount of water that will be introduced to the wood. Hot steam cools quickly and turns back to water. Water that has been infused with tiny particles of animal protein glue has a white-ish appearance. Ever seen those chalky looking rivulets inside your guitar? Guess what that tells you?
Actually, I missed my target on the first attempt, and had to re-drill. This why it is not a good idea to first determine that you are not going to be re-using certain components… it sets you up to be less careful.
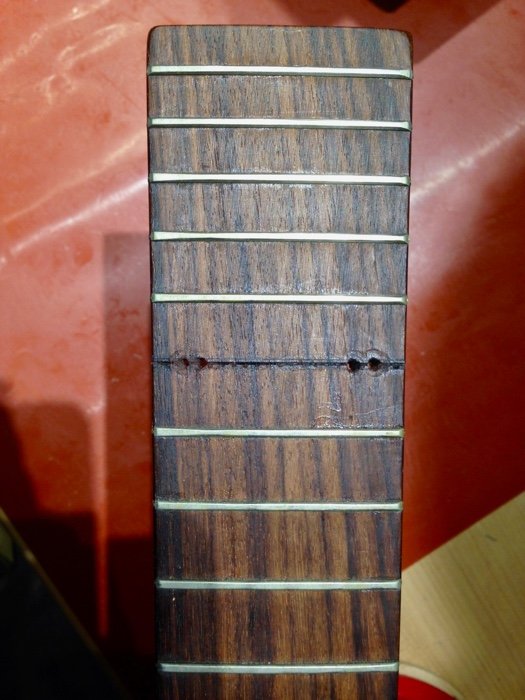
My first set of holes “Missed it by *that* much!"
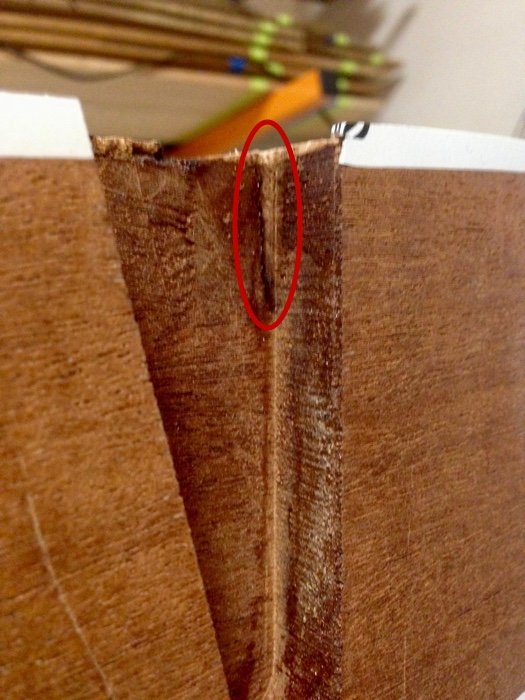
I removed the neck, curling the neck heel in the process. I had toyed with the idea of making a new neck for this guitar for a long time. I wanted to replace the twin compression rods with carbon fiber, and thin the grip substantially. This little mishap helped me make my decision… but I am getting ahead of my own story.
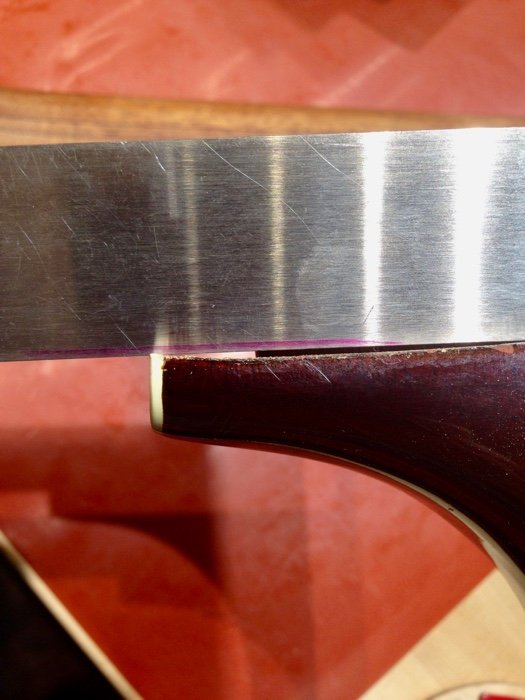
The fretboard extension is glued to the soundboard. When I remove a neck (such as for a neck reset), I apply heat to the area to soften the glue. Working slowly and carefully, using a spatula or two, I can work the bond loose between the (in this case) Spruce and the (in this case) Rosewood.
And sometimes you get a suprise under the lid:
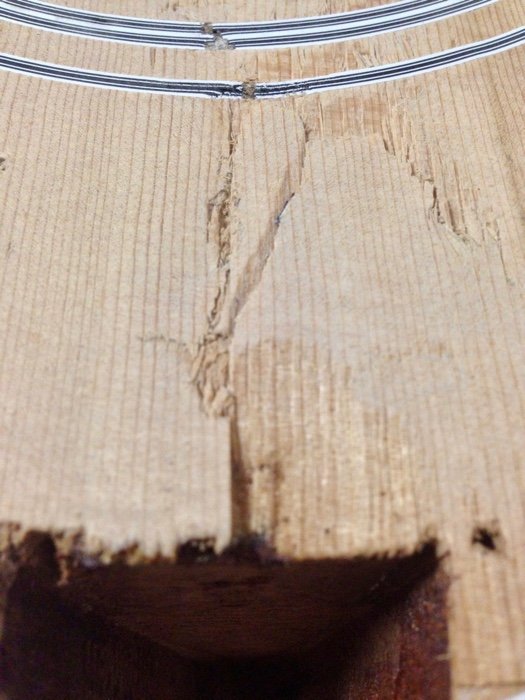
I am sure you are all familiar with the appearance of what we all lovingly refer to as “grain runout,” where one half of a soundboard looks darker that the other half (until you turn it upside down, and you see the reversal of the light/dark effect). Most of us can live with the aesthetic (or un-aesthetic) issue, but the greater concern of runout is structural integrity. The photo, above, shows how readily wood will release from itself when runout is severe, as I was so happy to discover was the case beneath the fingerboard extension. I knew there was something about this soundboard I didn’t like, something to account for its lackluster response. And that was before the shearing event occurred.
The guitar is now in two pieces: Neck and Body.